Metallic Structure / Parts Manufacturing
We are highly capable of supplying high precision products such as, Aluminum alloy machined parts, Fabricated Sheet metal Brackets, Plastics Injection Moulds, Pressure Die Casting dies, Machined Cams for different machine and process equipment applications, CNC turned parts.

Our Supplies caters to industries such as :
- Automobiles & Rail Industries
- Aeronautical Industries
- Pump and Valves Industries
- Marine Industries
- Earth moving Agriculture and Home products
- Metal Process industries
Machines & Equipments :
- CNC vertical machining centers
- CNC Turning Centers
- Conventional Milling and Turning Machine
Fiber Reinforced Plastic (FRP) part manufacturing
The multiple ranges of products manufactured with different manufacturing process with Glass fiber material to reach our customer requirements.
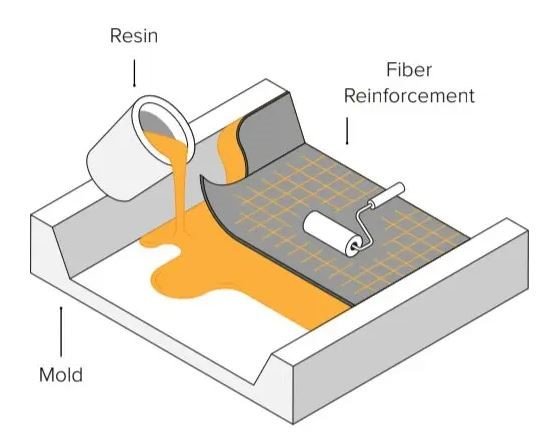
Wet / Hand Layup (HLU) / Contact Moulding
Our well trained engineers will select the best method for your project based on factors such as production volume, parts dimensions, budget, and other requirements. In the Hand (wet) lay-up or Contact moulding process, the fiber is cut and laid into the mold then resin is applied via a brush, roller, or spray gun. In this contact moulding enables us to produce innovative and cost effective parts for our customers, including Rail, Boats, Automotive, Domestic application parts. The process is best suited for one-sided finished parts and low volume requirements with considering minimum thickness of 3mm and radius 6mm.
LRTM (Light Resin Transfer Moulding)
With LRTM moulding, the dry fiber is inserted into a two-part mold. The mold is clamped shut before forcing the resin into the cavity at high pressure. It is usually automated and used for larger volume manufacturing. The process is best suited for high precision parts where a two-sided finish is required and this manufacturing process enables us to produce innovative and cost effective parts. (Resins used: Generally Epoxy, Polyester, Vinylester and Phenolic with considering minimum thickness of 3mm and radius 6-12mm).

Vacuum Bagging
The Vacuum Infusion Process, or VIP, is one of many closed mold processes. It distinguishes itself by being the only process that utilizes only atmospheric pressure to push the resin into the mold cavity. The mold cavity can be a one-sided mold with bagging film being utilized for the “B” side, a two-sided mold, or even a soft “envelope/ vacuum” bag.

- Higher fiber content laminates can usually be achieved than with standard wet lay-up techniques, resulting in stronger products.
- Better fiber wet-out due to pressure and resin flow throughout structural fiber, with excess into bagging materials.
- Lower tooling costs than other closed mold processes.
- The two main drawbacks of VIP when compared to other closed mold processes are slower cycle times and higher consumable costs.